Tilman, En pleine floraison
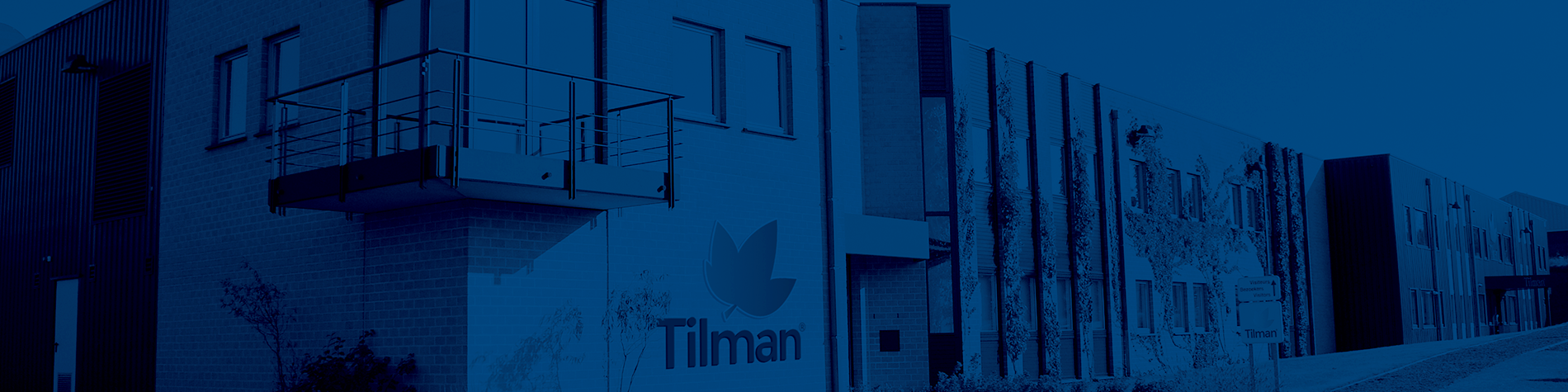
> Presse & Média > Tilman, En pleine floraison
Tilman En pleine floraison
Leader sur le marché belge de la phytothérapie, le laboratoire Tilman fabrique des solutions naturelles à base de plantes.
Une success story qui ne semblepas prête à s’arrêter !
Tout semble avoir infusé délicatement dans un premier temps. En 1956, la société Tilman & Cie est créée par le pharmacien Lucien Tilman.
Spécialisée dans la fabrication de tisanes, elle englobe une pharmacie, une droguerie et un laboratoire qui emploient trois personnes. Il faudra attendre 1984 pour que le laboratoire pharmaceutique Tilman soit lancé.
L’industrialisation démarre en 1990, avec l’achat de premières machines installées sur le site de Bomal (dans l’est de la Belgique). En 1998, est inaugurée l’usine de Baillonville, dans les Ardennes belges, qui doublera de taille en 2005 et connaîtra deux nouvelles extensions : la première, en 2012, pour accueillir des lignes de production de comprimés et de sirops, et la deuxième, en 2016, pour augmenter la surface des locaux de production.
Le laboratoire Tilman est présent à l’international, notamment en France, depuis 2021, date de rachat de la société de distribution pharmaceutique Promogen. L’offre hexagonale est pour l’heure dominée par deux fleurons, Flexofytol (complément alimentaire), pour le traitement de l’arthrose, et Sedinax (médicament), pour les troubles du sommeil. Elle est vouée à s’étoffer, avec l’introduction prochaine d’autres gammes, aujourd’hui leaders en Belgique.
Actuellement, le laboratoire Tilman emploie 210 salariés et affiche un chiffre d’affaires de 50 M€, porté par une croissance annuelle de l’ordre de 15 %. Le portefeuille de produits compte 80 références over the counter (OTC), dont huit médicaments. La plupart sont fabriqués par le laboratoire Tilman : les gélules, les comprimés, les sirops, les sprays et les tisanes en sachets.
Des produits hautement dosés. Le leitmotiv du laboratoire Tilman est de proposer des solutions naturelles à base de plantes : des compléments alimentaires et des médicaments de phytothérapie depuis la création du service R&D, en 2001. Leurs spécificités : des process de fabrication et des contrôles qualité identiques pour les deux catégories de produits ainsi qu’une haute teneur en principes actifs, qui garantit l’efficacité des formules, étayée par des études cliniques. « La phytothérapie peut être aussi efficace que les molécules chimiques, ce que nous démontrons via des études, actuellement au nombre de 21, publiées dans des revues internationales », explique Eric Lambert, directeur projet France. « Par exemple, nous avons réalisé une étude en double aveugle contre placebo, présentée au congrès européen de rhumatologie (Eular), pour le complément alimentaire Flexofytol : celle-ci a montré une sécurité d’utilisation et une activité comparable à des solutions de référence sur le marché », poursuit notre interlocuteur. L’objectif du laboratoire est de multiplier les études cliniques et de faire passer certains compléments alimentaires au rang de médicaments.
Deux zones d’activité. Au global, « l’usine se déploie en deux zones d’activité et 35 personnes sont postées à la production », résume Sophie Bandry, responsable de production. La zone sud, où se situe le siège et où sont stockés les matières premières et les produits finis avant leur expédition, s’étend sur 46 000 m2, dont 1 500 m2 alloués à la production. La zone nord est réservée à la fabrication des compléments alimentaires Flexofytol PLUS et Flexofytol FORTE, à base de curcuma. Au total, 15 lignes de production permettent d’assurer la fabrication et le conditionnement des compléments alimentaires et des médicaments. Les matières premières sont des plantes en extraits secs (poudre) ou fluides, des huiles essentielles et des excipients.
Formes solides et liquides. Après avoir été pes.és, ces diffèrents ingrédients sont assemblés d’après les formules des produits. Pour la fabrication des formes solides, les poudres de plantes et des excipients sont introduits dans un mélangeur, selon un temps défini. « Pour s’assurer de leur bonne homogénéité, les mélanges sont passés au tamis avant d’être de nouveau mélangés », reprend Sophie Bandry. En fonction de leur forme finale (gélules ou comprimés), elles sont introduites dans la géluleuse ou dans l’une des deux comprimeuses (qui impriment leur forme au comprimé grâce à l’utilisation de 30 poinçons inférieurs et supérieurs). S’ensuit le pelliculage des comprimés, qui leur donne leur couleur finale, au moyen d’une des trois pelliculeuses, avant leur mise sous blister. Pour les formes liquides (sirops en flacons, sprays), une cuve en inox à double enveloppe est utilisée pour chauffer puis refroidir les mélanges d’extraits fluides de plantes, d’eau, de sucre et de glycérine, une seconde cuve de soutirage servant à vider la cuve. Les liquides ainsi obtenus sont ensuite conditionnés sur une ligne de remplissage automatisée. Enfin, une dernière ligne de production est réservée à la fabrication des tisanes en sachets. Un projet d’agrandissement de la zone sud est dans les tuyaux, soit 6 000 m. supplémentaires. L’inauguration est prévue en 2025. L’objectif : « augmenter les capacités de stockage et moderniser la préparation des commandes et les expéditions », indique Sophie Bandry. ■
Carole De Landtsheer pour Pharmacien MANAGER – 04/06/2023